Risk management
The ability to manage risks is a key element of the company's governance and control. The Board of Directors has ultimate responsibility for risk management, while operational management lies with the Chief Executive Officer, the Management Team and other staff. Risk management is based on a code of conduct and several overarching policies. Strategic and business-related risks are discussed by Group Management and decided upon by the Board of Directors. Regular reporting takes place on financial position and compliance with the financial policy.
The company applies an iterative risk management process to identify, evaluate and manage risks at Group level. In this process, based on what is currently known, a number of risks have been identified and categorised in three areas of risk – operational, market and financial. The description of the various risks in each risk area does not claim to be exhaustive, nor is it ranked in order of importance. Not all risks are described in detail, and a comprehensive assessment must contain other information and a general assessment of external conditions. In addition, an in-depth analysis is presented of climate-related risks and opportunities linked to the operational risk of environmental impact and climate change.
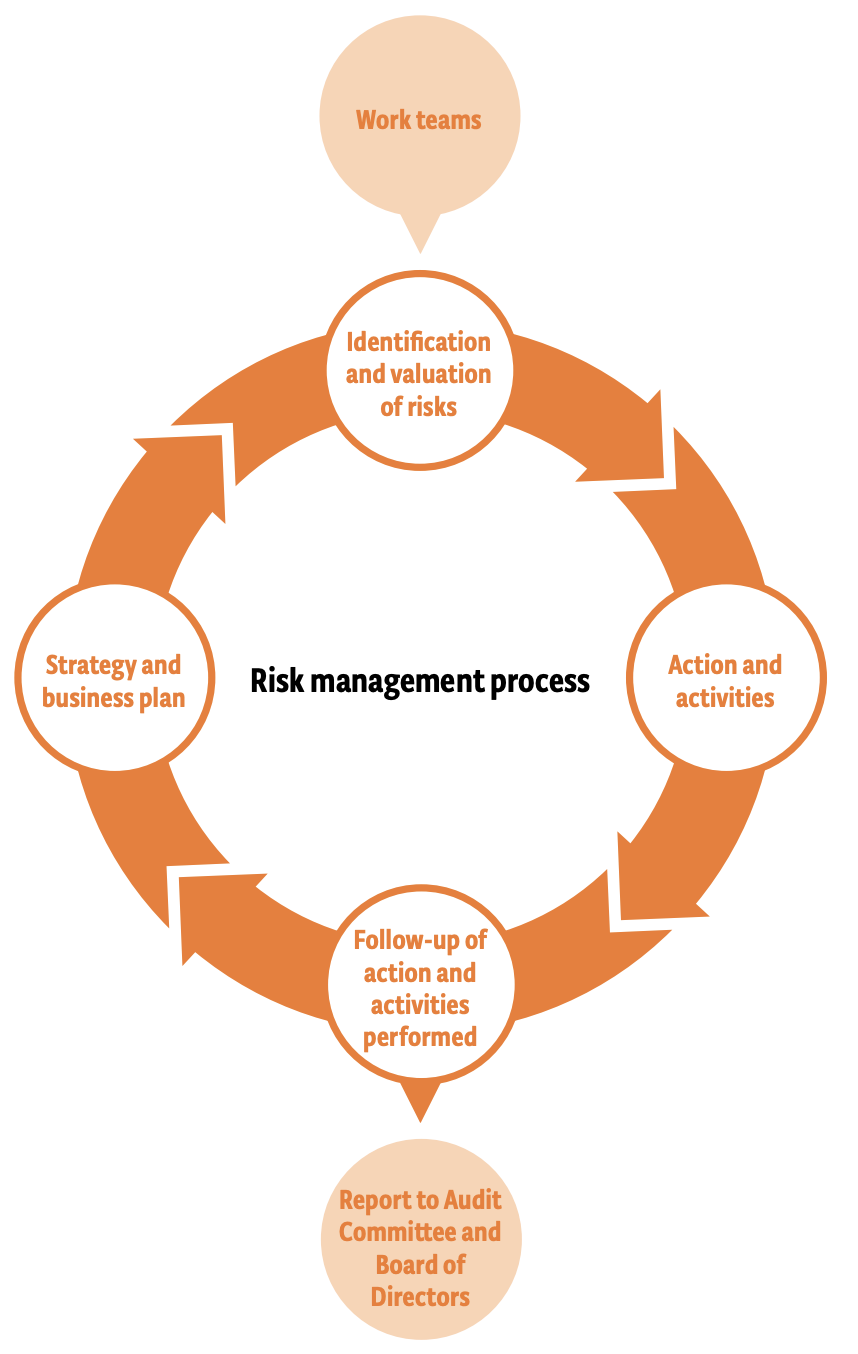
Operational risks
Description of risk
Midsona's impact on environment and climate represents a significant business risk that can have an impact on both reputation and financial results. There is also a risk of global environmental and climate change impacts affecting the result. Some of the most important sources originate from transport, water and energy consumption, raw material supply, packaging and production waste and food waste. Extreme weather, which is becoming more and more common, is a growing challenge for food production and therefore also for Midsona. A warmer climate is likely to lead to higher operating costs, for example through increased cooling requirements in production facilities. In addition, there is a risk that drought, hot weather, floods and cold may significantly reduce agricultural production, resulting both in price increases and difficulty in ensuring necessary volumes of raw materials (see also below under the risk factor raw material prices and raw material shortages. Negative climate impacts from fossil fuel-powered transport and fossil energy use to run operations are also risk factors. In all countries where Midsona operates, environmental legislation already exists, such as taxation of fossil fuels and plastics. Tighter climate policy, new regulations and changes in market conditions may affect parts of operations dependent on fossil fuels. If these risks materialise, it could lead to increased fossil fuel transport and energy costs, which in turn would adversely affect financial performance. Midsona is also dependent on access to clean fresh water.for the production of foods and cosmetics. Water shortages in countries where the company operates may affect performance. A high negative environmental impact or non-compliance with environmental requirements also risks damaging reputation and trust among consumers and investors.
Risk management
To manage the significant operational risks posed by Midsona’s environmental and climate impacts, work takes place continuously to implement a number of strategies and actions. These aim to reduce our environmental impact, ensure compliance with environmental requirements and improve our resilience to climate-related risks. Midsona has adopted Science Based Targets approved by SBTi to reduce its climate impact. Through clear governance and responsibility for our climate targets within Midsona’s management, our climate impact is also an integral part of the Company’s business strategies and financial planning.
We engage in systematic preventive environmental work at our production facilities and set environmental requirements for our carriers and suppliers. This includes ensuring that our partners comply with our high environmental standards.
One action taken to reduce our energy footprint is to use only 100% renewable electricity in our operations, which has already been implemented in the Nordics and North Europe divisions. In addition, a certain amount of renewable solar energy is produced in all divisions. Targets for the use of 100% fossil-free transport have also been set to achieve efficient and sustainable transport. To reduce our impact from waste, we have set targets to increase recovery and reduce food waste.
Midsona operates in countries with a relatively low risk of water scarcity, but we actively work to keep water consumption low. The Spanish business, which involves the most water-intensive production, has set specific targets and has taken action to lower its fresh water consumption.
In addition, we are closely monitoring developments in environmental and climate issues to gain important insights that may contribute to better informed decision-making and financial planning. This includes keeping up to date with new regulations and market trends that may affect our business.
Description of risk
As the business largely consists in developing, producing and selling organic products, health foods and consumer health products, it is crucial that business partners, investors and consumers associate the Company’s operations and brands with positive values, both a good reputation and credibility being vital in terms of business value and sales success.
Reputation and credibility may easily be damaged if Midsona, a supplier or a partner, for example, causes damage to the environment, exploits its workforce, produces harmful products or otherwise commits acts in conflict with the values that our brands represent, resulting in a negative sales trend and adverse impact on the Company’s earnings.
Risks associated with corruption may also damage reputation, which may affect business relationships and, by extension, profitability. Should these risks materialise, they might have an adverse impact on the business and earnings in the form of decreased sales, for example.
Risk management
We conduct systematic prevention work both internally and externally with partners through our Code of Conduct, Supplier Code of Conduct, policies and other guidelines for our employees to uphold the reputation of our company and our brands, with the right quality, functionality, product labelling and accurate market communications.
In relationships with suppliers, our Supplier Code of Conduct, the supplier’s self-assessment and an active partnership in terms of business ethics are the most important tools in taking responsibility for the value chain.
The Group also has a whistleblower policy in place, which everyone is encouraged to use if there is the slightest hint of corruption or breach of our business ethics.
Description of risk
The perception is that it has become more difficult and more costly in recent times to insure production facilities in the food industry. This difficulty is also exacerbated by the technical status of the Company’s production facilities.
Production facilities, production equipment and other assets may be damaged by fire, power outages and other physical risks in the wake of environmental and climate change, such as flooding. There is a risk that insurance cover for the assets may not be adequate. Inadequate insurance cover may negatively affect the financial position in the event of damage or loss.
An unplanned production stoppage may directly affect customer deliveries, as a high degree of production is order-based. Should this risk materialise, it may have an adverse impact on the Company’s financial position.
Risk management
We work with external insurance brokers to maintain well-balanced, cost-effective insurance cover for our assets in line with policy. An extensive range of insurance is maintained, covering property and business interruption insurance, transport insurance, financial loss insurance and third-party liability and product liability insurance.
The Company works systematically both to minimise the risk of incidents and to have contingency plans in place to limit the effects of possible incidents.
Description of risk
The business is dependent on a properly functioning and secure IT infrastructure. Disruptions or faults in critical systems have a direct impact on our production and distribution activities, as well as on our financial reporting.
This may be caused by system overload, lack of competence, external influences in the event of unauthorised access to, and hacking of, or physical damage to the infrastructure. Sophisticated data intrusion, cyberattacks, IT-related fraud and shortcomings in the handling of customer and employee information may be detrimental to financial capacity and reputation.
Risk management
We work continuously on keeping our IT systems well protected against attacks and intrusion and to improve the level of service with regard to the IT infrastructure, in line with policy, guidelines and procedures.
Processes were established to increase information security in and between systems. For example, investments are being made to improve recovery plans and data storage functions. Information security is monitored regularly through IT security audits.
The IT environment is centralised for better control and cost awareness, while at the same time working with local experts to ensure that we comply with all legal requirements.
Description of risk
Midsona is dependent on certain major suppliers, particularly in the health foods category, to enable it to secure its supply of goods in the short term.
If the agreement with a critical supplier were to be terminated prematurely or renegotiated on less favourable terms, or if a critical supplier were to declare bankruptcy or suffer extensive operational disruption, or if a critical supplier were to be adversely affected by external factors, there is a risk of disruption in the flow of goods, and sales capacity may be negatively impacted if Midsona is unable to replace the supplier at commercially acceptable prices within a reasonable period.
If deliveries are delayed, this may adversely affect commitments and relationships with customers, causing the Company’s customers to stop buying the Company’s products and/or, in some cases, to ask for refunds. If supplier risks were to arise, this may have an adverse overall impact on business, profit and the brand.
Risk management
To minimise risks in the supply of goods, we maintain close dialogue on volume-critical products with our major suppliers to ensure reliable delivery.
To reduce our dependence on individual suppliers, alternative suppliers are established, above all in connection with delivery-critical, volume raw materials. We assume responsibility in the value chain by cooperating with our suppliers in areas such as quality, safe raw materials and products, the environment, human rights and ethical enterprise.
We monitor, rate and follow up suppliers using our supplier assessment system. Suppliers are rated in terms of sustainability, quality and safety. The findings from the risk mapping increase awareness of our sustainability risks in the value chain, improving risk management and the capacity to focus on the risks that may cause us most harm.
In addition, this allows us to maintain better and more constructive dialogue with our suppliers and affords us opportunities to work with them to improve key processes.
Description of risk
The Group has eight production facilities: five for organic products, one for health food products and two for consumer health products. These are located in Sweden (1), Denmark (2), Finland (1), Germany (2), France (1) and Spain (1).
At the production facilities in Denmark (1), Germany (1), France (1) and Spain (1), substantial volumes of certified organic products are produced for own brands. Stoppages or disruptions in the production processes at any of the facilities, caused for example by fire, mechanical faults, technical disruptions, weather conditions, chronic climate change, natural disasters, labour market disputes or terrorist activities, may have an adverse impact in the form of direct damage to property.
Unplanned production stoppages may directly affect customer deliveries, as a high degree of production is order-based.
In addition, increased inflationary pressure — which would probably lead to higher interest rates and increased rental costs following index adjustments — combined with increased energy costs, would considerably increase costs at the production facilities.
Should the risks described above materialise, this would have a significant impact on the Company’s operations and earnings.
Risk management
For some volume products, production may be transferred to other machines. Machines are maintained continuously in accordance with established schedules, and major maintenance events are normally scheduled for the summer months.
Replacement investments are made according to a predetermined plan that the Group follows, and new investments are made when necessary.
We work with external insurance brokers to maintain well-balanced and cost-effective insurance cover for our assets. An extensive range of insurance is maintained, covering property and business interruption insurance, transport insurance, financial loss insurance and third-party liability and product liability insurance.
The Company works systematically both to minimise the risk of incidents and to have contingency plans in place to limit the effects of possible incidents.
Description of risk
Organic products and brands represent one of the cornerstones of the business. There is always a risk of serious product liability incidents.
Within the EU, there are common rules defining what is organic. For example, these rules describe how production is to be performed, how the products are to be labelled, how control is to be exercised and what the requirements governing imports of organic products from countries outside the EU are.
An important aspect of the checks on organic production is traceability, ensuring that goods can be tracked at the manufacturing stage and to ensure that they have been produced organically. This means that documentation and information on how products are manufactured are particularly important in ensuring that organic products are genuinely organic. Shortcomings and inaccuracies in such documentation and information may therefore have major consequences.
Handling of food and other products Midsona sells, such as medicines, is an important aspect of the business, imposing strict demands as to traceability, hygiene and handling. Shortcomings in product handling and safety checks may lead to contamination, allergic reactions, personal injury or other types of harm, which may damage the Company’s reputation and cause stakeholders’ trust in the Company’s products to be reduced, and may result in defective products having to be recalled or bought back.
Recalls may damage the Company’s reputation and become costly as a result of it not being possible to sell goods in stock. Product liability claims may also be made if a product is considered to have caused injury. Should such risks materialise, they may have an adverse impact on the Company’s reputation and earnings.
Risk management
Our aim is for our own production facilities to have product safety certification. We wish to take responsibility at all stages of the value chain by working with our suppliers in areas such as quality, safe raw materials and products.
We focus on supplier quality and product control as well as high social and environmental standards in the supply chain, with the aim of ensuring safe and sustainable suppliers. Our quality and purchasing functions have together identified the risks arising in the process, in order to ensure approved, safe and sustainable suppliers and manufacture of our products.
Our work on quality and product safety is guided by applicable legislation, official requirements, customers, industry guidelines and internal policies, procedures and instructions. Strict quality requirements apply in all processes to minimise the risk of shortcomings, product recalls and product liability claims.
Any complaint flows are captured early in our quality assurance system for a proactive response. Our products are certified to a large number of different standards. All set stringent requirements with regard to quality, environment and sustainability matters and serve as a stamp of quality on our products.
Our insurance solution includes third-party liability and product liability insurance to cover any product liability claims.
Description of risk
To fulfil its goals, Midsona is dependent its ability to recruit, retain and develop qualified and motivated employees. There is stiff competition for qualified staff.
Risk management
Through annual staffing, skills and succession planning, it is ensured that employees are recruited and that they stay and develop the right skills.
We focus continuously on making Midsona an attractive employer, where health and safety in the workplace, wellness, and market-based and competitive employment benefits are important parameters. A modern and attractive corporate culture is also an important factor in the recruitment of staff.
Description of risk
Legal risks include a number of different risks in partially separate areas. Changes in legislation, legal infringements within the business, maintenance of permits and certifications, and shortcomings in agreements entered into are some examples of legal risks that may have adverse financial consequences for Midsona.
Risk management
Midsona continuously monitors developments in upcoming legislation in a number of areas and, with external advisers, addresses any legal risks identified.
In addition, a systematic and controlled follow-up of permits, certifications and licences has been developed. Our legal, regulatory and quality organisations together manage existing and new requirements, laws and guidelines from government agencies, as well as the management of permits, certifications and licences in a quality management system.
Market risks
Description of risk
Customers are mainly pharmacy, grocery and health food chains that also offer competing products sold under their own brands, so that many customers can also be regarded as competitors to some extent.
In our view, these operators are not dependent on individual brands and can hold back price increases, making increased marketing initiatives necessary. If these operators widen their product ranges under their own brands, this may lead to further competition and increased price pressure.
Should these risks materialise, the impact on earnings would be substantial, mainly in the form of decreased sales.
Risk management
We work actively on development and innovation of our brands to earn the place of each brand on the shelf in shops and, at the same time, to convey a clear and accurate message to consumers at the point of sale.
The customer’s and consumer’s trust in our brands is of crucial importance to our competitiveness and long-term development. Without strong trust in the Company’s brands, it would be very difficult to capture market shares and to grow.
Reliable development, innovation and sustainability processes foster conditions for gaining and retaining the trust of customers and consumers.
Description of risk
Consumers change their buying behaviour and new consumer trends come and go. There is always a risk that changes in consumer behaviour, or when new trends arise, are not seized upon in time, leading to a loss of competitiveness vis-à-vis competitors.
If competitors are better at monitoring consumer behaviour and new trends, there is a risk that Midsona will lose competitiveness. Should this risk materialise, the impact on the Company’s earnings, in the form of reduced sales, would be substantial.
Risk management
To help people live a healthy life, it is vital that we recognise trends and changes in consumer behaviour early. This requires knowledge of trends, consumer behaviour and product content.
We believe we have well-developed practices and processes for actively monitoring external developments and identifying new consumer behaviour and trends. We attend major trade fairs in Europe and North America, read and analyse trend reports, and buy market data on our local markets.
Description of risk
Midsona purchases raw materials, such as cereals, rice, nuts, almonds and fruit, mainly from suppliers in Europe, South America and Asia. Both the supply of raw materials and raw material prices may be affected by strong demand combined with low supply, or by other external factors beyond the Company’s control, such as agricultural policy decisions, subsidies, trade barriers, increased energy prices, military conflicts, acts of terrorism, crop yields, events on commodity exchanges and the cost of manufacturing the raw material.
Normally, price reviews take place once a year. However, higher prices for raw materials may require Midsona to further raise its product prices over and above customary price revisions. It may be difficult, generally, to have price increases passed on to customers directly. In special cases, discussions are held with customers continuously during the year in the event of a dramatic rise in the price of a raw material.
If Midsona does not succeed in passing on a price increase to its customers, there is a risk that this will adversely affect margin. Another risk is that the Company will be affected by a shortage of raw materials if suppliers are unable to supply the quantities ordered.
Risk management
We continuously monitor the trend in prices for all important raw materials to stand a good chance of contracting volumes at the best possible time. To ensure both access to and the price of key raw materials, supplier agreements are normally signed covering the requirement over the six to twelve months ahead.
Midsona usually charges higher raw material prices at the next stage by raising the prices charged to customers. Several key raw material purchases are coordinated at the European level by our supply chain organisation. By purchasing large volumes, it is possible to influence raw material prices to a certain extent.
Financial risks
Description of risk
Financing risk refers to the risk of future capital procurement and refinancing ofmaturing loans becoming difficult or costly
Risk management
To ensure that, in all situations, the Group has access to the necessary external financing at reasonable cost, the rule is that confirmed credit commitments must have an average remaining term to maturity of not less than 12 months.
The financing agreement with Danske Bank and Svensk Exportkredit was extended for another year on unchanged terms. Following the extension, it will run until September 2026. At year-end, the average remaining term to maturity on confirmed loan commitments was 16 months.
Description of risk
Liquidity risk refers to the risk of not being able to fulfil payment obligations when they fall due, as a result of an inadequate supply of liquid funds.
Risk management
To control and plan for the Group’s cash requirements, the Group economy and finance function uses liquidity forecasts that the subsidiaries submit on a monthly basis for the six months ahead.
A financial contingency must be maintained in the form of a liquidity reserve, comprising cash balances and unused credit commitments, which must correspond to not less than 7.5 percent of the Group’s forecast annual sales. The liquidity reserve was in the range of 12.9–16.9 percent of net sales in 2024.
In addition, the liquidity reserve must, at all times, exceed the sum of the Group’s loan maturity for the next six months.
Description of risk
Transaction exposure is the risk that affects the Group’s earnings and cash flow through the operational and financial transactions that are effected in currencies other than the functional currency of each Group company.
The Group’s sales of goods are mainly made in the companies’ local currencies, although the currency flows arising from purchases, primarily of goods, in other currencies give rise to the Group’s current transaction exposure.
Risk management
Group Management has been mandated to currency hedge goods purchases in USD with currency forward contracts as a result of the increased currency exposure in USD/DKK and USD/EUR. This is particularly the case for supplier contracts with predefined payment schedules.
Forward exchange contracts are market valued at each balance sheet date. The maximum exposure is USD 4.5 million at each balance sheet date.
Currency risks are otherwise to be managed in supplier and customer agreements through currency clauses. In order to reduce the impact on earnings from changes in exchange rates, Midsona continuously uses price adjustments for customers and suppliers based on the changes in exchange rates.
Description of risk
Interest rate risk refers to the impact of a change in interest rates on earnings. How quickly a change in interest rates affects earnings is determined by the fixed-interest period for credit and investments.
The Group is a net borrower and does not invest in listed instruments. As a result, the Group’s interest-bearing liabilities to credit institutions represent the main exposure to changes in interest rates. Most interest-bearing liabilities to credit institutions are subject to variable interest rates.
Risk management
The Group strives to strike a balance between a reasonable ongoing expense for its borrowings and the risk of a significant negative impact on earnings from a major change in interest rates.
At present, the guidance is not to hedge interest rate risks in the Group. As a result, changes in the market interest rates have an impact on the financial cash flow and earnings. The average interest rate on the Group’s bank loans and overdrafts in 2024 was 5.9 percent.
Description of risk
There is a risk of losses if counterparties with whom the Group has cash and cash equivalents or financial investments are unable to fulfil their obligations; this is known as a financial credit risk.
Another risk is that our customers cannot fulfil their payment commitments; this is known as a customer credit risk.
Risk management
Rules for how surplus liquidity is to be managed are established in a policy. The Group is a net borrower, and surplus liquidity is to be used to reduce loans from credit institutions.
In March 2024, a voluntary additional repayment of liabilities to credit institutions of SEK 79 million was made in connection with existing credit lines. The Group’s subsidiaries are required to place surplus liquidity in bank accounts in the Group account system or in bank accounts approved by the Group economy and finance function.
The Group’s counterparties in financial transactions are credit institutions with good credit ratings. Customer credit risk is managed continuously by each Group company via credit checks and internal credit limits per customer. Bank guarantees or other sureties are required for customers with low creditworthiness or insufficient credit history.